What Is Galvanising?
Exploring the Process,
Benefits & Applications of Galvanising
What Is Galvanising?
Hot-dip galvanising (HDG) is a process that involves immersing steel into a kettle (often referred to as a bath or tank) filled with molten zinc for corrosion protection. This inherently simple method has distinct advantages over alternative solutions for protecting steel against corrosion. During immersion, a chemical reaction between the steel and zinc creates an alloy coating that offers unparalleled protection. Hot-dip galvanising adds durability and longevity to steel products by protecting against corrosion for many years to come.
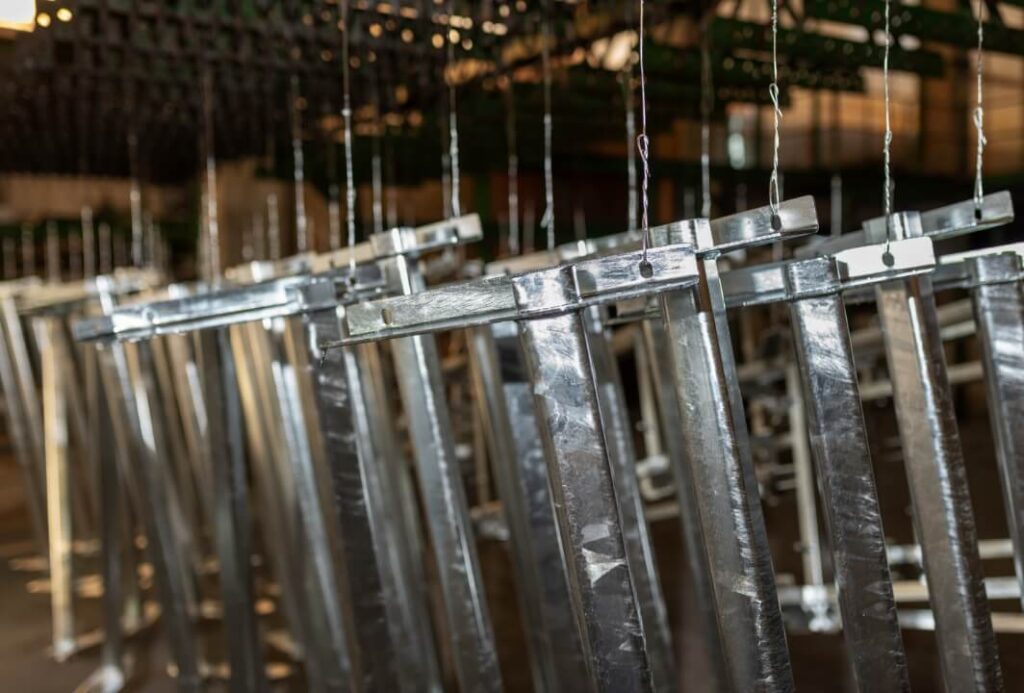
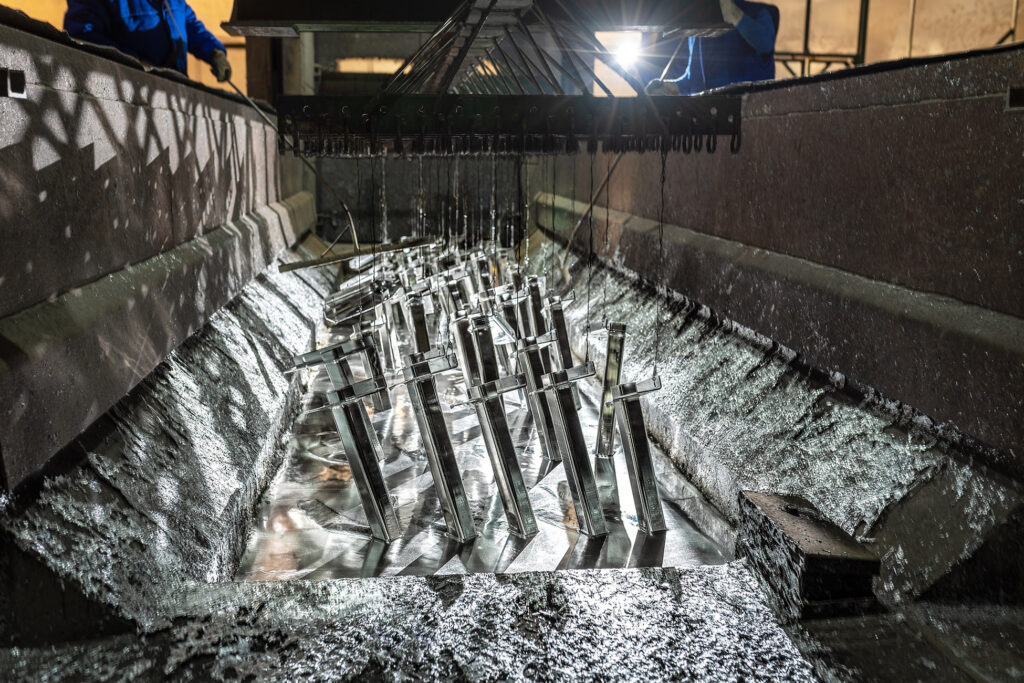
Hot-dip galvanising opens up an abundance of opportunities for protecting steel against the effects of corrosion. By carefully understanding its unique properties and processes, hot-dip galvanising provides a powerful corrosion protection method that ensures long-term and sustainable structures for various applications.
The History Of Hot-Dip Galvanising (HDG)
To gain an in-depth knowledge of hot-dip galvanising and its history, one should go back all the way to 79 AD and start at its inception.
-
Galvanising is said to have begun around AD 79. Records show zinc being used for ancient construction projects, marking the beginning of its commercial use.
-
Galvanising in modern history dates to 1742 when P.J. Malouin, a French chemist, presented several experiments involving coating iron with liquid zinc at the Royal Academy of Sciences.
-
Luigi Galvani, the namesake of galvanising, discovered the electrochemical process that involves metals while conducting an experiment involving frog legs in 1772.
-
Alessandro Volta made important advances in galvanising research when he discovered the electro-potential between two metals, creating a corrosion cell.
-
During a pivotal experiment, Michael Faraday made a groundbreaking discovery regarding the sacrificial action of zinc. Faraday conducted a series of tests involving zinc, salt water, and nails in this remarkable scientific exploration.
-
The ingenious French engineer, Stanislaus Tranquille Modeste Sorel, pioneered the early galvanising process. He secured a patent for this ground-breaking innovation.
-
For the production of galvanised steel, the British galvanising industry had a substantial annual zinc consumption of 10,000 tons. This remarkable quantity of zinc played a vital role in meeting the growing demand for galvanised steel and highlights the significant scale of operations within the industry.
-
Shortly after, the United States witnessed the opening of its inaugural galvanising plant, albeit slightly later than its counterparts. During this period, the galvanising process involved the meticulous hand-dipping of steel into the zinc bath.
-
The continuous march of progress in metallurgy and furnace technology has propelled significant advancements in the efficiency and sustainability of the galvanising process.
-
Zinc consumption for hot-dip galvanising steel production in North America has reached remarkable heights, surpassing 600,000 tons annually. This significant amount is divided between two main processes — approximately 200,000 tons for the batch after-fabrication method and an astounding 400,000 tons for the continuous galvanising method — and its ubiquitous application across various industries and applications where iron or steel finds use. Galvanising has long been recognised for its proven corrosion control solutions in diverse fields such as utilities, chemical processes, pulp and paper production, automotive manufacturing, and transportation. These industries have long used galvanising to protect assets against corrosion — this trend remains strong today! Hot-dip galvanising has an enviable track record and remains an invaluable solution to corrosion protection in various metal components and structures worldwide. Thanks to its superior performance and reliability, hot-dip galvanising has cemented itself as one of the premier corrosion prevention methods today.